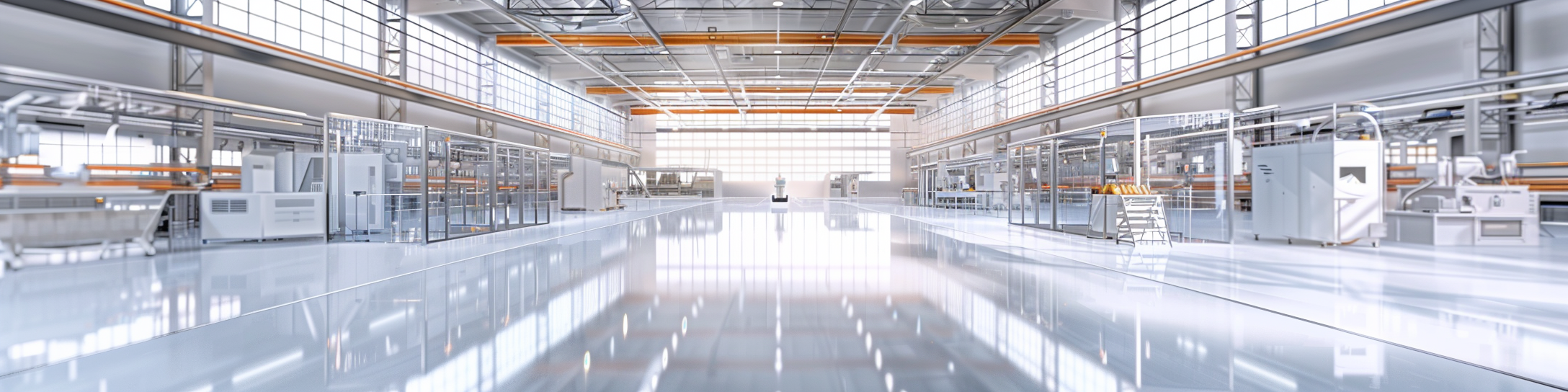
Custom Engineered Heat Trace Solutions
Are you having issues with busted pipes or frozen surfaces? Not particularly familiar with heat trace systems? We can help! We’ll give you the details on everything there is to know about heat trace systems and heating cables, and we can solve your problems and design solutions.
Self-regulating heating cables can be used to protect pipes from freezing, maintain process temperatures for liquids, heat tanks, melt snow on roofs and surfaces, provide instant hot water at the tap and even to heat floors.
As an inventor of self-regulating heat-tracing technology, we have designed and deployed millions of feet of heat trace in more than 20 countries around the globe.
For nearly a century, people everywhere have relied on variations in electric trace heating for temperature protection. Heat trace utilizes electricity and insulation to maintain or increase the temperature of pipes or other vessels, replacing any heat lost to outside temperatures. A heat trace system protects pipes and tanks from freeze damage while maintaining ideal temperatures to ensure that you never have to sacrifice efficiency to heat loss.
Existing initially as MI cables producing heat from electrical current creating resistance, this original technology lacked control and adjustability. Almost 50 years ago the first production of “cut-to-length” trace cable was made available. Between then and now, strides in technology have seen trace heating systems develop from mineral-insulated metal sheathed cables (MI) to the self-regulating heat trace cables available today. Self-regulating heat trace cable offers a self-limiting and cut to length solution
that makes up the bulk of today’s market. These heat trace systems offer solutions for anything from pipe protection to soil warming.

Inefficient heating processes can waste huge amounts of energy, slow down or interrupt business or production when systems break, costing you both time and money. Damaged products caused by freezing temperatures or improper heating is a painful mistake. Heat trace systems are built to make sure that mistake is never made. Improperly designed heat trace leads to comments like “We HATE our Heat Trace!”.
We solve issues with problematic heat trace systems! “We LOVE to fix Heat Trace that you HATE”
In the cold winter months, pipes transporting liquid substances can become vulnerable to freezing temperatures and increased viscosity. Heat trace is most commonly used to protect pipes from freeze damage during winter conditions. These systems are most often used to keep water from freezing, as water in any process or facility is critical.
Additionally, heat trace allows for optimal control of the flow and viscosity of transported liquids, allowing the user to regulate the temperature within pipes, in turn enhancing and streamlining your work.
Protecting pipes from freezing isn’t the only use, though. Here are some other common uses:
- Snow melt systems on sidewalks, driveways, and patios
- Keeping tank contents from freezing
- Helping instruments operate in more favorable ambient conditions.
- Maintain Hot Water Piping System Temperatures
- Protect Piping and Piping Systems from Freezing
- Maintain Process Piping, Vessel, Components and Systems Temperatures.
Whatever your need is, we can provide a solution as our in-depth understanding of heat trace systems will help you select the weather protection option that is right for you.
Heat Trace Frequently Asked Questions
What does a typical heat trace system look like? A completed system begins at a power source. The heat trace cables are placed along the entire length of the surface of a pipe, sometimes held in place normally with a high temperature 8tape. Once attached, both the pipes and heat cables are covered with an insulation jacket to minimize heat loss. Heat trace systems can be controlled with a simple thermostat, or with a temperature sensor like an RTD that provides feedback to a more common PID or PLC style controller. These systems will control and adjust the temperature of the heat trace. Additionally, most are equipped with varying types of monitors to assist the user in observing power output. Most heat cable purchased independently can be cut to the desired length, then combined with termination and splice/tee kits2 to complete the system.
Note: Heat trace power output is measured by watts per linear foot. Heat trace voltages range from 120 to 277 Vac, and from 3 to 20 watts per linear foot.
In today’s marketplace, there are providers of materials using one heat trace technology. Understanding that there are numerous ways to heat a system; the key is that it is done right at each installation. CTS is in the unique position where it can provide the right heat trace technology to every client, whether that technology is Self-Regulating, Constant Wattage, Mineral Insulated, Power-Limiting, Skin-effect Tracing, Impedance, Induction, or Circulating Fluid Tracing (i.e., steam, hot oil, or glycol). Through relationships with various heat trace manufacturers and the refinement of select heat trace technologies, CTS offers a complete spectrum of heat trace solutions. This includes, but is not limited to, Self-Regulating and Power-Limiting cable, Mineral Insulated cable, Skin-Effect Trace Systems, as well as controls and monitoring solutions Designed and Built by CTS.
As evidence by the above and the fact that our relationships with all industry leaders in their respective heat tracing fields are long term, it is clear that this team provides the greatest value for your Heat Tracing Dollar. Our controls are patented and designed to be the most energy efficient possible.